on Chloride Penetration:
- Roads & Traffic Authority NSW (Aust.) (CTI Consultants) “The (Caltite) hydrophobic pore-blocking additive performed very well, especially at the deeper intervals where chloride reductions in excess of 97% were recorded. These results are better than those for the organo-silanes, probable due to the presence of the hydrophobic additive throughout the concrete rather than only in the outer layer as is the case for the post-applied sealers”
- “Based on these results, (Caltite) can be used to protect concrete against moisture and chloride ingress unde conditions of atmospheric exposure.”
- Vicroads – Concrete Materials Tedchnology Dept. State Government of Victoria, Aust. “The HPI (Caltite) concrete has been found to outperform both conventional and SCM’s (slag, silica fume) concrete with far greater reductions in Volume of Permeable Voids (VPV). (Caltite) is an excellent material for reducing the VPV of conretes.”
- Engineering and Water Supply Department, Govt. of South Australia – “(EVERDURE CALTITE) can be of enormous benefit in sustaining and prolonging the life of a concrete structure.”
- CTI Consultants for Roads & Traffic Authority of New South Wales (Aust). – “The (Caltite) pore-blocking hydrophobic additive performed very well, especially at the deeper intervals where chloride reductions in excess of 97% were recorded. These results are better than those for the organo-silanes, probably due to the presence of the hydrophobic additive throughout the concrete, rather than only in the outer layer as is the case for the post-applied sealers.”
- City of Glenelg, South Australia – “Recent inspection shows the CALTITE concrete to be still quite sound (after 20 years), whereas the normal concrete shows severe aggregate exposure and areas of cracking due to steel corrosion.”
- Taywood Engineering Ltd, UK – “Cores taken from CALTITE concrete exposed to tidal immersion for up to 17 years showed no signs of corrosion of the embedded reinforcing bar and little surface erosion of the cement matrix.”
- TROW, Canada – “The EVERDURE CALTITE mix meets the performance expectations of a latex modified concrete with regard to chloride penetration.”
- Institute TNO, Netherlands – “Intrusion of chlorides by diffusion of seawater transport is diminished by the use of CALTITE.”
on Water Penetration:
- Queen’s University, Belfast – “Amongst the three modified concretes covered in this paper, (10% & 20% silica fume and Caltite), CALTITE concrete was observed to be the most efficient in reducing the water permeability.”
- British Board of Agrément, EEC – “Everdure Caltite System forms a suitable alternative for compliance with ..BS 8007 :1987, BS 8102 :1990 and BS 8110 :Part 1:1985”
- Dr. Adam Neville, UK – “The use of Everdure Caltite in concrete as an alternative to the application of a membrane to the surface of the concrete seems to offer considerable benefits”
- National University of Singapore – “W4 (Caltite) was the only waterproofer, indeed, the only product tested, which dramatically reduced both pressure penetration and water absorption”
- “This mix (containing EVERDURE CALTITE) is thus recommended to make concrete “water-tight””
- Taywood Engineering Ltd., UK – “The water repellency of CALTITE concrete was found to be unaffected by tidal immersion over a period of up to 17 years.”
on Chemical Attack:
- Hardman Chemicals P/L, Australia – “Our EVERDURE CALTITE Joint-free acid proof floor is now 19 years old in constant use – which compares extremely well with the life of our ordinary (concrete) earliest floors.that were destroyed in less than 9 months each.
- Coal Products Limited, UK – “I can advise that your EVERDURE CALTITE SYSTEM concrete is still in a satisfactory condition. Surrounding bases cast using a grade 30N/mm² concrete with SRC are now showing extreme degradation due to continuous acid attack.”
- Gudgeon, Mott, Hay, Anderson (Singapore) – “We are pleased we used your “CALTITE” and other additives for these (fertiliser) floors and we must compliment you on a product that more than lives up to your specification.”
- Brisbane City Council, Australia – “Both samples suffered from sulphide attack, but the sample containing CALTITE and PLASTET No. 2 suffered much less attack than did the ordinary 20Mpa concrete”.
- Sandberg, UK – “The CALTITE specimen exhibited significantly less acid attack in terms of both depth of attack and area of deterioration.”
- University of Toronto, Canada – “The mix containing EVERDURE CALTITE admixture showed a marked improvement in the ability of concrete to endure severe environments.”
on Other Properties:
- University of Liverpool, UK – “The resistivity measurements show that the modified (EVERDURE CALTITE) concrete is considerably less conductive than the unmodified concrete.”
- Taywood Engineering, UK – “Compared with conventional concretes, the values of resistivity were very high, particularly after soaking. For concrete with a typical moisture content of 3 – 5%, resistivity values are in the range of 50 k.ohm.cm. The Caltite concrete had a resistivity in excess of 1,000 k.ohm.cm, i.e. more than 20 times higher than conventional concrete”
- Sandberg, UK – “The expansion of the prisms of CALTITE concrete under freeze-thaw conditions was considerably lower than that of the control at all times during the 50 cycle test; the visible spalling was also considerably less and occurred later than on the specimen of control concrete.”
- Ready Mixed Concrete, Hong Kong – “We have carried out exhaustive laboratory tests on concrete containing CALTITE and have found it to have no detrimental effects on strength development.”
- BRITISH BOARD OF AGRÉMENT (BBA) (*Ask your Cementaid representative for a copy of the certificate) – “The Caltite System has no detrimental effects on the properties of the cured concrete. ..Site observations and other data show that the properties of concrete containing Everdure Caltite have been maintained for up to 30 years.
- “Petrographic analysis of concrete containing a known reactive aggregate showed no reaction in concrete containing the EVERDURE CALTITE System when subject to wetting and drying cycling.”
- “Significantly greater resistance to carbonation.”
- “The System has no detrimental effects on the properties of the cured concrete.”
- “Site observations and other data show that the properties of concrete containing EVERDURE CALTITE have been maintained for up to 30 years.”The effects of the Caltite System ingredients are permanent. Independent testing on Caltite concretes after up to 20 years field exposure to severe chloride and sulphate environments, has proven no reduction of these outstanding properties, or the quality of Caltite concrete and embedded reinforcing, at all.
Case Studies – Long Term Performance:
Engineering & Water Supply Department; Government of South Australia
In 1960, un-reinforced OPC concrete pipeline support chairs for BHP were cast in a salt pan in Port Pirie, Spencer’s Gulf, South Australia. (1:2:4 mix, @ approx. 280Kg / m3)
Groundwater Analysis:
sulphates @ 7,200 mg/Lt.
chlorides @ 53,000 mg/Lt
After less than two years, all of the ordinary concrete chairs suffered severe sulphate attack.
Additional chairs were cast in 1962 using exactly the same mix, but incorporating Everdure Caltite @ 30 Lts / m3, as well as steel reinforcement.
After 18 years in service, the reinforced Caltite concrete has remained in excellent condition, with no re-bar corrosion, and only minor surface etching. The Caltite concrete remains in service today, corrosion-free after 37 years. This is in contrast to the non-Caltite chairs, which were severely damaged within only 4 years, and near to collapse after 20 years, as shown to the right.
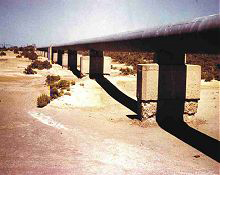
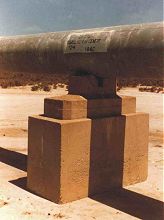
With Caltite after 18 Years
(Photo 1980)
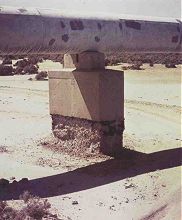
Without Caltite after 20 Years
(Photo 1980)
Port Wakefield, Spencer’s Gulf, SA –
Artillery Range Markers (Dept. of Defence)
The chloride resistance of Caltite concrete is time-proven to be effective over the long-term by the Australian Department of Defence Artillery Range Markers in Port Wakefield, South Australia, in the Spencer’s Gulf region. The Caltite concrete used an Ordinary Portland cement content of 400 Kg /m3, and a water /cement ratio of 0.45
These were placed in the inter-tidal zone in 1968 to restrict public access, and are subject to daily tidal immersion cycles in the highly saline water of the Gulf.
In normal concretes, elevated drying temperatures such as those here greatly increase rates of salt penetration and of re-bar corrosion.
In 1985, after 17 years wet / dry cycling, cored samples were tested by drilling and measuring actual chloride penetration at varying depths.
Compared to the surface level (0 – 10mm), chloride penetration in the 10 – 25mm zone was reduced by 84%. Chloride reduction beyond the 10 – 25mm zone was 100%.
Examination and testing of these and other long term marine exposed Caltite structures by Taywood Engineering Ltd. confirmed the following;
- “Cores taken from Caltite System concrete exposed to tidal immersion for up to 17 years showed no signs of corrosion of the embedded reinforcing and little surface erosion.
- Compared with conventional concretes, the values of resistivity were very high, particularly after soaking. The Caltite concrete had a resistivity in excess of 20 times higher than conventional structural concrete.”
- The capillarity of field “Caltite” concrete with an average cement content was lower than low w / c ratio lab concretes containing over 450 Kg/m3 of cement and superplasticisers.
- The water repellency of “Caltite” concrete was found to be unaffected by tidal immersion over a period of up to 17 years”.
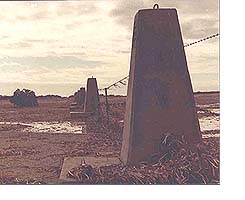
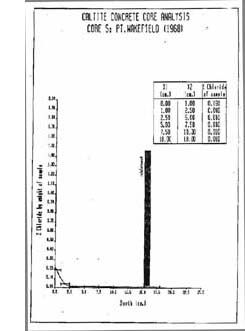
City of Glenelg, SA – Boat Launching Ramp
This project demonstrates long term evidence confirming that the high electrical resistivity of Caltite concrete provides an additional preventative protection against chloride attack. This is the case even where chlorides are present at the level of reinforcement prior to final set (e.g. beach sand, contaminated aggregates, etc.), such as in this project.
In 1965, the City of Glenelg (South Australia) re-constructed a corrosion-damaged boat launching ramp, this time using Everdure Caltite concrete for the lower, seaward section, to prevent chloride attack. The Caltite concrete used a 25 MPa mix with an Ordinary Portland cement content of approx. 280 Kg / m3. The upper portion (photo foreground) used exactly the same mix, only without Caltite.
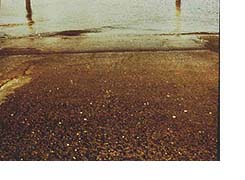
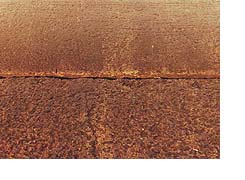
PHOTO: 1985 (after 20 years)
Caltite section remains in good condition.
After 20 years, the section without Caltite shows evidence of severe chloride attack, with large cracks and patched areas over reinforcement lines (left of photo), as well as 8 – 10mm surface loss from salt scaling, so that the larger aggregates are clearly exposed.
By contrast, the Caltite concrete section has remained in very good condition, with no evidence of re-bar corrosion attack, and insignificant surface wear.
Being at the seaward end of the ramp, the Caltite section is subject to a shorter inter-tidal drying period. At the construction joint however, drying exposure conditions are equivalent, and a valid comparison of performance is provided.
The adjacent photo (1985) shows the construction joint between the Caltite (top) and plain concrete (bottom), after 20 years exposure. The Caltite concrete has remained in excellent condition, and it is still possible to see the “broom-marks” made at the time of finishing, to provide traction. On the other hand, severe surface loss, aggregate exposure, and evidence of corrosion-induced cracking, is clearly visible in the plain concrete.
Chloride analysis of the Caltite concrete section in 1985 by Taywood Engineering confirmed no corrosion of steel reinforcement, despite inclusion in the Caltite mix of a calcium chloride accelerator at the time of casting, to prevent wash-out by the incoming tide. This resulted in a very high “background” level of chlorides, being present within the concrete from the day of casting.
This background level was approximately 4 times higher than that required for activation of steel, yet no corrosion had occurred, despite 20 years tidal exposure.
The absence of corrosion is primarily due to the low moisture content and very high electrical resistivity of the Caltite concrete.
Commenting on the extraordinary durability performance of the Caltite concrete, the researchers commented;
“Compared with conventional concretes, the values of resistivity were very high, particularly after soaking. For concrete with a typical moisture content of 3 – 5%, resistivity values are in the range of 50 k.ohm.cm. The Caltite concrete had a resistivity in excess of 1,000 k.ohm.cm, i.e. more than 20 times higher than conventional concrete”
The chloride profile in this instance shows an ingress “curve”. Unusual for Caltite concrete, (see Pt. Wakefield Artillery Markers, above), this is believed to be due to the presence of a crack in the slab at the coring location, (which had subsequently self-healed), and the fact that the Caltite concrete was “cured” in sea-water.
The Caltite ramp remained in service and in similarly good condition until middle of 1999, when the structure was de-commissioned, and the area subsequently re-developed.
The Caltite ramp achieved the Clients’ requirement for a corrosion-free and maintenance-free service life of their marine exposed structure, being in this instance 34 years. This included daily wetting and drying under hot, salty and windy conditions, at least one known crack, and the presence of a very high level of admixed chlorides at the level of reinforcement since the day of casting.